
Sandeep Mistry
Gokul Suryamurthy
(Sep 2018 - Dec 2018)
Design Problem Statement:
Existing Gimbal system in market were bulky and huge in size to bear 1 - 4 Kg of payload which led to novel refinement of Gimbal design being compact,reliable, robust and required strength to bear LIDAR and camera payload weighing up to 4 Kg.
PROTOTYPE 1 FOR UAV

PROTOTYPE 2 FOR UGV

Individual contribution:
Prototype 1:
-
Executed sheet metal design of pitch shoulder with 45 degree bends at two point.
-
Created flat pattern out of Al 6061 and implemented brake press for bending Al sheet metal.
-
Tested the prototype by manual balancing 1.5 Kg of payload and aligning it with the CG of system.
Prototype 2:
-
Designed pitch platform for 3 Kg of payload by appropriate material selection using Al 6061 and redesigned it through topology optimization.
I fabricated both the prototypes through Brake press, CNC and Knee mill.
3D model: Prototype 1 & 2


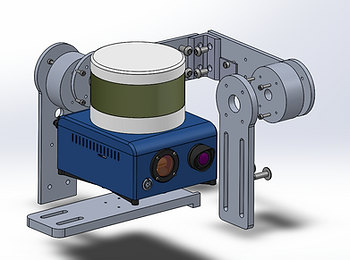
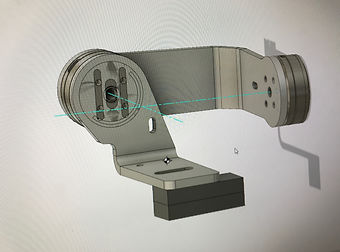
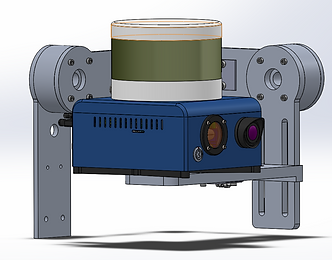
Fabrication: Prototype 1 & 2:


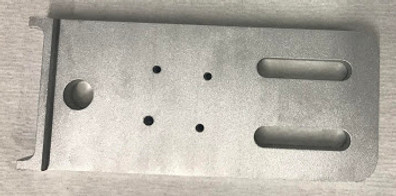

Balancing & testing Prototype 1:

FEA Analysis & topology Optimization:

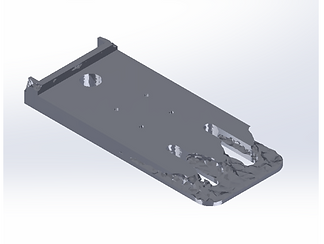
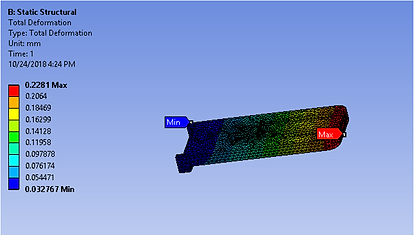


Future work:
-
Implementing Flex and Rover Hammer Impact test to detect structural rigidity with FEA results and modal frequency to avoid structural failure at resonance respectively.
-
Integrating the optimised Gimbal assembly in UAV and UGV and testing the data accuracy captured by LIDAR and multiple cameras in 1m x 1m span range, vertical & 100 % slope inclination environments to succeed in Physical testing category of DARPA's Subterranean challenge.